Seeing the Light: Upperroom Dallas and the Future of Construction Technology
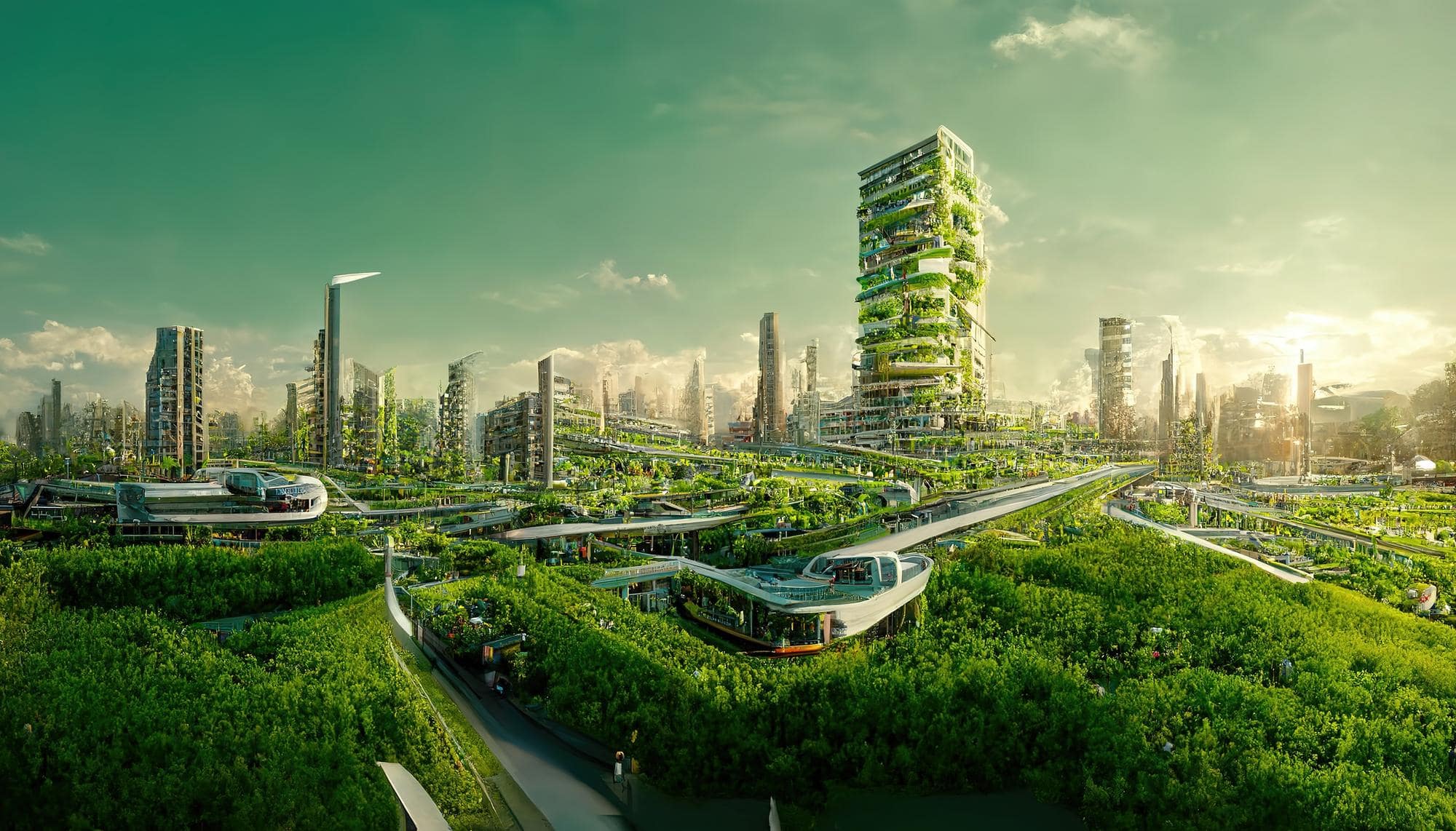
Imagine a future in which you don a headset to enter a virtual-reality simulation of a construction site before it exists. A future in which a robot analyzes a space slated for renovation, recording each minute detail, from measurements to materials, in a fraction of the time and cost it would take humans to do the work. And imagine that, in that future, the world of creating buildings is so friendly to its human workers that language barriers are no longer an issue, with in-ear translation technology that allows people to communicate onsite, hands-free, in real time.
Advances like these would be game-changing—life-changing, in some instances.
And they’re here today. Welcome to UPPERROOM Dallas, a Rogers-O’Brien Construction church-renovation project, where the future of construction is happening now.
FROM VET CLINIC TO WAREHOUSE
But first, let’s go back to 2010, when UPPERROOM was a humble worship group renting rooftop space from a veterinary clinic in the Oak Lawn area of Dallas, a diverse neighborhood dotted with clusters of older homes. From there, the group moved on to leasing a converted paintball facility. The church’s new space in south Dallas, a converted warehouse scheduled to open its doors in March 2024, will be “more than just a church,” say members of RO’s team who worked on the renovation, with a multiroom day-care center, a fully equipped recording studio, a coffee shop and other amenities. It will be a place to worship, a place to create music, a place to hang out—a place to live.
What happened between 2010 and now? One obvious answer: the pandemic. “During the COVID lockdowns in 2020, the church was online and got up to a million followers,” says Adam Minter, Rogers-O’Brien’s superintendent for the project. As UPPERROOM increased its online presence, it began to post videos of moments from worship services on YouTube, where followers praised what they saw as the group’s authentic and relatable style.
While many of those followers weren’t local—during the pandemic, they came from all over the world—the church wanted a place to gather for those who were. The warehouse needed to be transformed into something bigger and bolder. Enter Dallas-headquartered Rogers-O’Brien, which worked with Overland Partners as the conversion project’s architect. RO’s team includes Minter; Richard Anderson, project manager; and general laborer Luis Romero.
Together, they embarked on a $16-million mission to expand the warehouse’s original 18,000-square-foot space to 28,500 square feet, with a prayer room that can hold at least 1,650 people, a child-care center, the coffee shop and 11 restrooms.
VR: REVIT, 3DS MAX, TWINMOTION
The UPPERROOM project embraced the future from the outset, with RO’s virtual design and construction team making use of virtual-reality platforms to help plan and execute portions of the construction process. Specifically, they used Revit, 3ds Max and Twinmotion to create an immersive virtual experience that simulates the finished space.
Jesse Brinkley, VDC specialist for the project, walks us through the process: “Our VDC team creates the building model in Revit. The visualization team then adds that model to 3D software, such as 3ds Max, to prep it for VR. This includes cleaning up geometry, creating UV shells and assigning color ID. Once the model is prepped, we use Twinmotion to add final touches such as textures, animated humans and vehicles, furniture, plants and lighting. We also use OSM [Open StreetMap] or photogrammetry data to help add in the real-world environment that would surround the building.”
Once these steps are completed, the virtual space is ready to welcome visitors. “We then use the Twinmotion software, along with an Oculus headset, to allow VR exploration of the finished environment,” Brinkley says.
HP SITEPRINT ROBOTIC LAYOUT
Even when RO’s team was ready to don their hard hats and break ground on the project in the real world, much of the work remained in the realm of the futuristic. They used HP SitePrint, a robotic layout solution, to assess the previous site before beginning its renovation. The little yellow robot, which resembles an especially fancy remote-controlled toy car, mapped out 15,000 square feet of wall layouts, wall-type tags, AV receptacles, fire-protection hangers and heads, door swings and door tags, as well as the hardware schedule—in just one day’s work. (You can watch a video of SitePrint at work on RO’s LinkedIn and Facebook pages.) The robot is controlled by a Trimble robotic total station.
The team raves about the time, cost and effort the robot was able to save on the project. “It took the guesswork out of the process,” Minter says. “The robot laid out everything, down to the paint colors; everything was captured, seamlessly and with no errors, and on schedule.”
And, of course, SitePrint “works sun-up to sun-down, regardless of weather, and never gets sick,” Anderson says. “All we have to do is refill the ink.” Anderson notes that a solution like this can be especially timesaving for high-rise buildings or other projects that feature repetition.
PROCORE: THE CENTER OF THE STACK
Sometimes what makes the future better is less about things like robots and virtual reality—and more about technology that simply makes processes, well, simpler. The RO team uses Procore’s suite of project-management solutions for everything from billing and scheduling to change orders, granting instant access to key information to everyone who needs it, and speeding up communication and erstwhile-bureaucratic processes that could sometimes add days or longer to project timelines. The software works with DocuSign, which allows team members to sign documents virtually.
Anderson is particularly impressed by Procore’s ability to streamline how his team handles change orders—no small thing, given that, as of early December, there had been 170 of them associated with the UPPERROOM project. “It allows us to track changes and keep the project transparent,” Anderson says, “so we all know exactly where we stand cost-wise at any given moment.”
Anderson describes how exactly Procore’s software has transformed RO’s change-order process: “Say you had additional steel requirements.
Previously, you would manually write out the request, turn it into a PDF, then you’d have to email it, you’d print out and scan things.” Now, he says, “I could see a need for more steel, sketch out what I need, take a photo with my phone, upload it—and in a couple minutes it could be on its way. That efficiency alone is staggering. A task or request that took a week to 10 days in the past can be completed the same day sometimes.”
He adds: “The ‘Change Event’ tool has allowed us to quickly and seamlessly identify additional scope gaps, design development and field changes. Typically, the cost for these types of changes would be absorbed by RO, but the tool allows us to easily identify whom we can pass the additional cost on to in a timely manner.”
The RO team working on UPPERROOM made use of a broad swath of Procore’s suite, Anderson notes: “We used everything except Workforce Management and Bidding/Estimating. All other tools, such as Project Management, Financials, Quality and Safety, etc., are heavily used.” He adds: “As far as our technology goes, we would say Procore is at the center of our tech stack and really enhances our technology program. We heavily use Procore’s RFIs, Submittals, Drawings and Specs.”
For UPPERROOM, the results of this seamlessness went beyond quantifiable facets of the project such as cost and timeline. “It allowed our team members to be very motivated,” Anderson says. He notes that the Procore software RO uses is “user-friendly” and hasn’t required team members to undergo special training or seek help from a specialist—but nonetheless, the company has become adept enough at making use of the latest construction technology that it received Procore’s 2023 Groundbreaker Award for Excellence in Innovation.
“We have a unique relationship with Procore and have been involved in some of their new initiatives,” says Nicholas Vargo, an RO project manager who acts as a liaison between the company and Procore. “They visit our sites to see how we’re using their technology, and we work together with them on committees and groups.”
That’s part of Procore’s approach to helping companies “make the technology an integral part of their daily workflows,” according to Kris Lengienza, vice president of global partnerships and alliances for Procore, regardless of their size. “While some companies on a larger scale may have dedicated teams managing technology rollout and adoption, Procore stands out for its inherent user-friendliness and support, making large, dedicated technology teams less necessary.”
TIMEKETTLE TRANSLATION EARBUDS
RO’s commitment to technology extends to individual trade professionals working on the Texas jobsite, many of whom speak Spanish as their primary or only language. Overcoming language barriers can be a challenge, with only partial or time-consuming solutions available until recently. Factor in high-volume noise from construction machinery—and a lot has gotten lost in translation.
Enter Timekettle’s Translation Earbuds, which translate speech in real time without the intermediary of a smartphone or human translator. RO used Timekettle’s WT2 Edge devices, which provide one earbud for each of two people in a bilingual conversation. The device boosted efficiency onsite with Luis Romero, a highly valued Spanish-speaking temporary laborer whose enthusiasm continually impressed RO—to the point where they brought him onboard as a permanent employee. “This technology has really given me a voice to communicate with people whom I previously would not have had the opportunity to,” Romero says. “It has also allowed me to understand a lot more of what I am being asked to do every day, which has given me more ownership and responsibility of what I do.”
The UPPERROOM project is RO’s first introduction to the possibilities of real-time translation technology. Anderson says its success has led to plans to roll it out for other projects.
NEW BUILDING MATERIALS
The UPPERROOM project demonstrates that innovation doesn’t just apply to processes and systems. RO also applied clever solutions and made use of innovative materials to expand and enhance the church’s renovated warehouse space. For example, while the original warehouse consisted of 18,000 square feet of area, RO’s team added a second floor without lifting the building’s existing roof, expanding the overall square footage to 28,500, with a final building height of 19 feet—a solution designed by the project’s architect, Overland Partners.
Anderson touts the team’s use of cross-laminated timber for this purpose, a solution also proposed by Overland. “We were able to add a second level without lifting the roof using CLT panels, because these panels were only five inches thick,” he says. “The panels have structural properties, and not only act as the ceiling system for Level 1 but are also the sub-floor system for Level 2. The panels weighed between 500 to 4,000 pounds each, totaling 135,000 pounds.
“These were all installed using low-clearance lifters, as we had an existing roof in place,” Anderson says. “By sandwiching the wood together, we were able to create the second floor without losing much space—we only lost about five inches of space due to the unique use of materials.” The Prayer Room, or sanctuary, is able to hold more than 1,650 people due to that upper floor.
In addition to the sanctuary, the expanded warehouse features a child-care center with five rooms for young children and two larger rooms for older children and teens, 11 restrooms, plus a fully equipped coffee shop and recording studio—where members can create more music and moments to spread their message to new followers. “All of the wood we used was sustainable,” Anderson says. “We were able to create a nice contrast between the look of an industrial warehouse, like you see in a lot of minimalist spaces, and beautiful natural materials.”
Anderson recognizes the impact of both design and structure for the project: “We added a large structural wood canopy that we think will become an iconic symbol for UPPERROOM throughout Dallas and other regions. It’s approximately 8,500 square feet and also made entirely of CLT panels, which were nine inches thick. Each of these panels weighed between 7,000 and 11,000 pounds, for a total of 275,000 pounds.”
Regarding the canopy, Anderson says it serves both a functional and symbolic purpose: “Functionally, the canopy serves as an outdoor room that can be used year-round, rain, hail or shine. It creates a transition for people outside the Prayer Room portion of the building without feeling isolated from the inside of the building. It allows the church to double their capacity when utilizing both the indoor and outdoor spaces at the same time. And aesthetically, the size and openness of the structure is to provide people with a greater sense of invitation, with open arms into the church and building.”
THE FUTURE IS SCALABLE
While next-generation construction technology is often dismissed as being out of reach for all but the most deep-pocketed companies, the RO team is hopeful that the products and solutions they’ve used on the UPPERROOM project can be realistic options for companies of all sizes. For example, the Procore software they use can be accessed on standard tablets and smartphones, which are already found in many workers’ backpacks and pockets.
It’s also worth noting that RO’s construction team for the UPPERROOM expansion consisted of three main members, who were able to work as efficiently as larger teams on other projects. Vargo, the project manager, touts the ability of contech platforms to be deployed on an a-la-carte basis to fit a company’s needs. “For example,” he says, “a company might have its own accounting system, but could use Procore to track other aspects of a project.”
The HP SitePrint robot, while requiring an upfront investment (RO paid about $45,000, Anderson says), cuts down on the number of workers needed to assess and prepare a site. “There’s a labor shortage here in Texas,” notes Laurel Dicus, RO communications manager. “Using HP SitePrint took just one operator, versus two to three people doing the job manually.”
The cost savings could make this solution attractive to companies with smaller budgets as well. “It cost about 11 cents per square foot for the robot to do layout, so we were looking at about $3,000 for 28,000 square feet,” Anderson says. “When you compare that to five or six people, even working 50 hours a day, at about $50 an hour, you’d be looking at around $25,000.”
RO pays about a $600 annual subscription fee to use Timekettle’s translation technology (the earbuds themselves run about $300), which places it within the realm of possibility for smaller companies. In fact, many times a vital factor in whether a company can “futurize” is simply a willingness to embrace new technology and other improvements. “The industry is changing,” Anderson says. “It’s becoming more sophisticated.
“Construction is viewed as a rough field, with old techniques and technology,” he continues. “But that’s about to change. We’re getting to a point where if you don’t use the new technology, you’ll get left behind.”
The smartest construction companies in the industry already get their news from us.
If you want to be on the winning team, you need to know what they know.
Our library of marketing materials is tailored to help construction firms like yours. Use it to benchmark your performance, identify opportunities, stay up-to-date on trends, and make strategic business decisions.
Join Our Community