Environmental product declarations: a sustainability step-change for construction
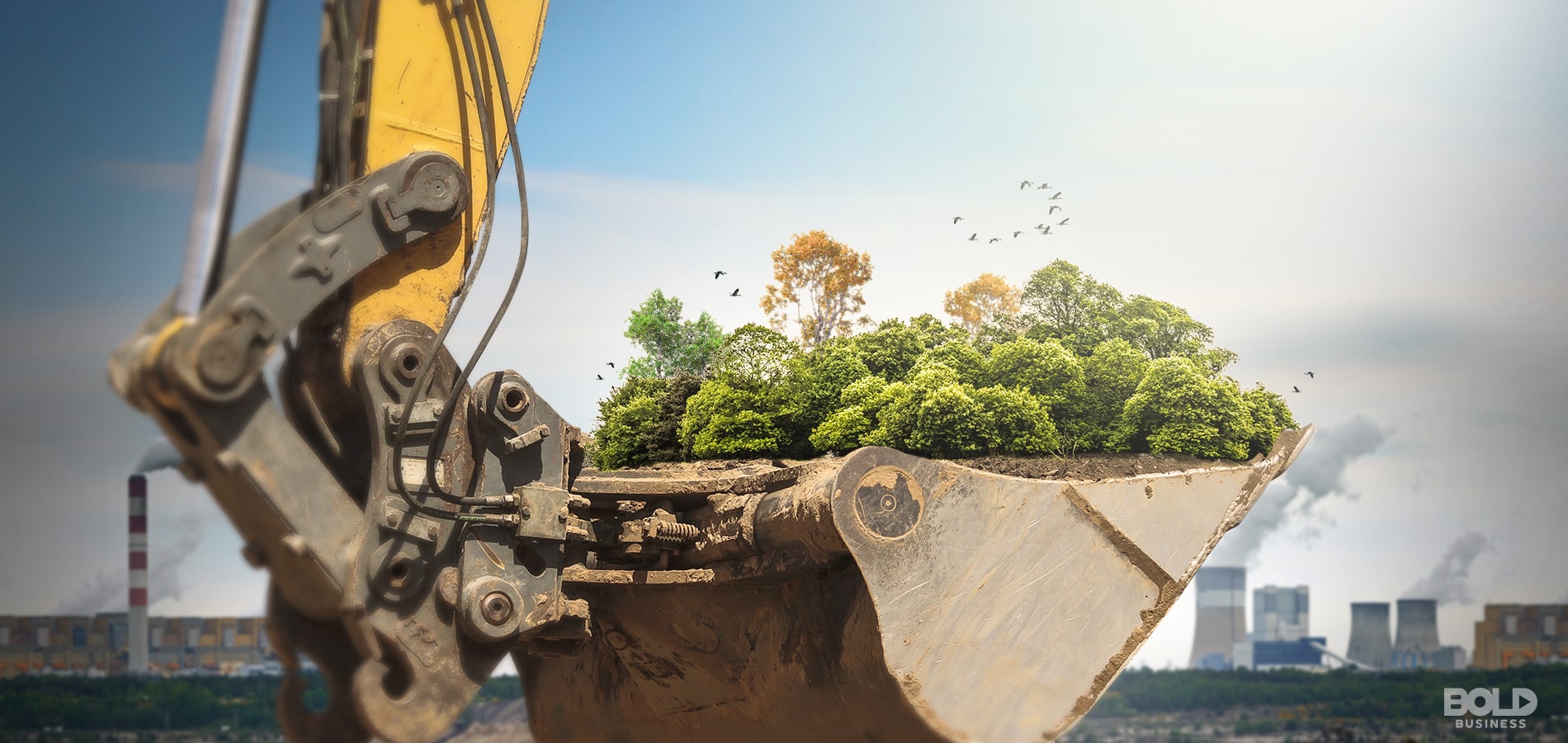
With more and more focus on sustainability within construction and the whole life cycle of a building, engineers and specifiers are often looking for ways to evidence sustainability. Could Environmental Product Declarations (EPDs) be the answer?
The construction sector has been dialling up its approach to sustainability for decades, adding new resources to the sustainability toolkit year-on-year. Environmental Product Declarations (EPDs) are one of the latest additions helping specifiers to advance sustainability goals. Used to compare and assess the environmental impact of products, they’re bringing transparency and choice to the construction market.
Wavin LCA project manager Matteo Tagliaferri explained that EPDs are comprehensive, standardised reports that detail the environmental impact of a product. They’re created using Life Cycle Assessment (LCA) methodology, which measures, among several impact categories, CO2 emissions throughout the product’s life - from raw material extraction through to transport, manufacturing, application, and end-of-life use, including recycling potential.
Based on the ISO 14040 and 14044 standards, LCAs give an understanding of a product’s environmental impact, measured against nineteen potential impact categories. This assessment is then used to create an EPD based on EN 15804+A2 which excludes any commercially sensitive information. Both the EPD and LCA are verified by an independent expert against strict protocols.
In the plastic pipe sector, for example, one of the most relevant impact measured is Global Warming Potential (GWP) in kg of CO2-eq. The GWP is an indicator of potential global warming due to emissions of greenhouse gases to air.
Thanks to the specifics and controls around their creation, EPDs are recognised as a standardised baseline for product comparison. By offering transparent, objective information about products’ carbon footprints, water footprints and energy consumption, they help consumers and regulators to make more informed sustainability comparisons and decisions.
Tagliaferri said: “EPDs are credible and reliable because they use a consistent, science-based measurement and always include third party verification.”
“In line with the saying ‘if you can’t measure it, you can’t manage it’, transparency is now a watchword for organisations committed to sustainability. With the construction industry regularly hit by ‘greenwashing’ claims, and the concept of carbon offsetting losing favour due to a lack of efficacy, it’s more vital than ever that sustainability initiatives are backed with scientifically based, quantifiable evidence. Better yet, standardising this reporting so that products can be easily compared will result in more effective sustainability choices and accelerate the journey to net zero.”
Already, countries like Denmark require transparent emissions reporting within construction. All buildings over 1000 m2 will require an LCA from 2023, with specific product data provided via Environmental Product Declarations (EPDs) preferred by the Danish Agency for Housing and Planning. While mandatory EPDs are potentially years away in the UK, there are clear signs that regulators are turning their attention to this area – and that’s going to spell changes for construction professionals.
The construction industry is awash with information about the carbon intensity of industrial products, and urgently needs to simplify and streamline sustainability information. This was highlighted in the first Building to net zero: costing carbon in construction report, that called on the Government to introduce “measures requiring suppliers who wish to make an environmental claim about a construction product to produce an EPD to substantiate it”.
The report further tasked the government to streamline access by encouraging “development of a centralised national database of EPDs and, through its own procurement practices require the collection and publication of EPDs. [This] EPD database should be digital, freely available to end users, and user-friendly.” It even suggested the introduction of a scheme to support businesses with the cost and administrative burden of creating EPDs, so the entire sector could be included in this environmental uplift.
The Government’s response broadly embraced these recommendations as they reflected its desire to see more regulatory support for more robust environmental measures in the construction industry. Its response recognised the success of mandatory EPDs in other jurisdictions and acknowledged that EPDs could provide the solution to its COP26 commitment to require “the disclosure of embodied carbon emissions of structural materials… used in major public construction projects, starting no later than 2025”. The Government also pledged to explore options to reduce the burden of EPDs on small and medium-sized enterprises - another indicator that these declarations will become increasingly important in years to come.
Government backing of EPDs in the future makes sense, particularly given its Net Zero commitments. In its Promoting Net Zero Carbon And Sustainability In Construction Guidance Note it outlines that “for the UK to meet its statutory climate targets, including its carbon budgets, requirements are only likely to increase in their stringency. Thus, being forward thinking and innovative, especially on high-value construction projects, is in the interests of both the government and industry.”
As more EPDs hit the market, specifiers, architects and developers are better able to understand the environmental footprint of their construction projects and completed buildings. These insights enable the creation of more materially efficient and environmentally friendly buildings.
Making informed product choices at the specification stage can reduce buildings’ CO2 footprints, as well as emissions and operating costs throughout their lifecycles. Considering EPDs when selecting building materials for a new development helps to support internal sustainability initiatives and ensure compliance with external targets. Directly comparing products using EPDs is also a credible way to prioritise ‘green’ building materials, that can contribute credits towards green building certifications such as BREEAM or LEED.
These credentials are positive differentiators in today’s market, and a powerful way to raise your organisation’s profile and demonstrate your environmental commitments. Sustainability accreditations like these can also support tender bids and enable developers to charge a ‘green’ price premium for their builds on the property market. With buyers today increasingly willing to pay more for sustainable builds, this premium fuels price hikes of between 11% and 25% across both commercial and residential construction in the UK and Europe.
With this premium up for grabs, there’s a strong incentive for construction professionals to interrogate every aspect of a build’s CO2 footprint. Transparent, standardised measurements across all three Scopes enables this and encourages all members of the supply chain – from manufacturers to logistics – to step up their sustainability efforts. Products and systems that are lighter, more efficient and easier to install, for example, mean the developer in charge of the project is able to lower their emissions by requiring less transport, fewer products and a reduced level of carbon-intensive installation equipment like excavators. EPDs are also important when it comes to controlling building waste. By offering end-of-life scenarios, they help to encourage the re-use and recycling of building materials.
“There are lots of ways we factor sustainability in. A lot of our products are made from recycled materials and we’re constantly developing more efficient products. This is key because using less has a knock-on effect – less waste, fewer deliveries, fewer repairs and so on.” Adam Salt, BIM Coordinator, Wavin
Developers who want to stay competitive in the market need to start prioritising EPDs in their supply chain. Specifiers should therefore make every effort to liaise with manufacturers who provide EPDs specific to the product they are thinking of using, so that they can select the most sustainable options for their projects.
The smartest construction companies in the industry already get their news from us.
If you want to be on the winning team, you need to know what they know.
Our library of marketing materials is tailored to help construction firms like yours. Use it to benchmark your performance, identify opportunities, stay up-to-date on trends, and make strategic business decisions.
Join Our Community