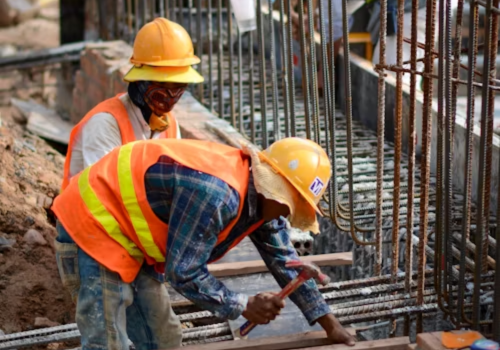
PROVIDENCE – The impact of tariffs on the residential construction industry is a complex issue, with varying effects depending on materials, supply chains, and specific manufacturers.
At the JLC Live Residential Construction Show held at the Rhode Island Convention Center, manufacturers, suppliers, and distributors weighed in on how tariffs will reshape the industry.
Wood and Asphalt Shingles Hit Hard
For manufacturers like TAMKO, which produces asphalt shingles, tariffs could mean higher costs for consumers.
“The park will serve as a catalyst for revitalization and social interaction, fostering greater unity within the community through exercise, relaxation, stress reduction, and enhanced mental well-being for all,” said Priscilla Meadows-Norwood, President of the Capitol View Neighborhood Association.
The key issue is the source of asphalt oil, which primarily comes from Canada. Unlike American oil, which is considered too rich for asphalt shingle production, Canadian oil is essential for manufacturers.
.jpg)
“TAMKO can either absorb the cost increase or raise prices,” said Stephen Hartnett of TAMKO. “Since all asphalt shingle manufacturers rely on Canadian oil, it’s likely that all companies will adjust their prices accordingly.”
Additionally, Canadian manufacturers exporting to the U.S. will face even higher costs due to tariffs on finished products.
The Impact on Wood Suppliers
Wood products, a staple in residential construction, are also being affected. Much of the wood used in U.S. residential construction is sourced from Canada, meaning tariffs will drive up prices.
John Evans of Weyerhaeuser, a major wood supplier based in New Hampshire, explained that while their structural components are manufactured in the U.S., a significant portion of raw materials comes from Canada.
Decking and Composite Materials Less Affected
.jpg)
Not all sectors of the construction industry will see major price increases.
Exhibitors at JLC Live who specialize in decking materials reported that they largely expect to remain unaffected. Many composite decking manufacturers source raw materials and conduct production entirely within the United States, avoiding additional tariff-related costs.
For example, one company utilizes rice husks from a nearby farm, while another produces deck planks using crushed limestone and plastic, all sourced domestically.
Uncertainty in Commercial Construction
Beyond residential construction, the commercial construction sector is also grappling with the potential ripple effects of tariffs.
Skanska Executive Vice President Bryan Northrop described the situation succinctly: "Uncertainty is a great word" to define the current state of affairs.
Skanska is working closely with clients to determine where material costs might increase, whether substitutions are possible, and if opting for American-made alternatives could offer any cost advantages.
However, if the entire construction industry pivots toward U.S.-made products, shortages and longer lead times could become an issue.
“If everybody in construction goes purely toward American fabricated, we'll have shortages on products or longer lead times,” Northrop warned.
Even if domestic materials become the go-to alternative, the increased demand is expected to drive up prices, potentially offsetting any savings from avoiding tariffs.
What Comes Next?
The long-term effects of tariffs on the residential construction industry remain uncertain.
“We’re still kind of in the infancy of all this,” Northrop added, underscoring that future price changes and supply chain adjustments will depend on how the market adapts over time.
For now, builders, suppliers, and manufacturers must navigate a shifting landscape, weighing cost increases, supply chain adjustments, and potential material substitutions to keep projects moving forward.
Originally reported by Wheeler Cowperthwaite in The Providence Journal.
The smartest construction companies in the industry already get their news from us.
If you want to be on the winning team, you need to know what they know.
Our library of marketing materials is tailored to help construction firms like yours. Use it to benchmark your performance, identify opportunities, stay up-to-date on trends, and make strategic business decisions.
Join Our Community