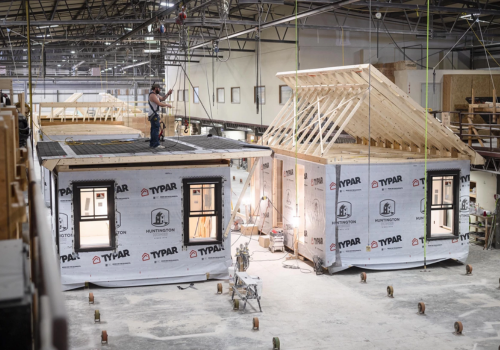
Vermont is experiencing a housing shortage so severe that many are wondering if factory-built homes could provide a solution. In East Montpelier, Huntington Homes has been constructing homes on an assembly line in a 100,000-square-foot factory. These homes begin as basic “Lego blocks,” which, once completed, are shipped and assembled into fully functional houses. “We can build a whole house in 12 eight-hour shifts — so, 96 hours,” said co-owner Jason Webster. The approach has allowed the company to streamline construction, reducing the time it takes to build a house from months to just a matter of days.
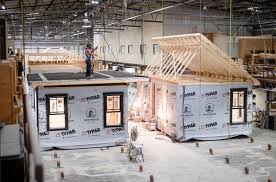
Vermont’s housing crisis is reflected in the state’s low construction rate, with only about 2,000 homes built last year—far below the 8,000 units the state needs to meet demand. Housing prices and rents continue to rise, and officials are struggling to meet the need for more affordable housing. The idea of utilizing factory-built homes, which include modular and manufactured housing, has gained traction as a potential solution to speed up construction and lower costs.
The benefits of this method are clear. By using standardized designs and building homes in factories, construction can take place year-round, including during Vermont’s cold winters. Additionally, it reduces the need for multiple subcontractors, such as electricians, plumbers, and roofers, who typically work at different times on a job site. All these workers are under one roof, leading to a more efficient construction process.
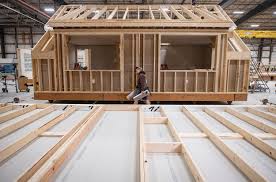
Housing researcher Jeff Lubell noted, “If we build one home at a time, it’s about the least efficient way you can do anything.” Mass-producing homes in a factory setting allows builders to take advantage of economies of scale, which can reduce costs. By ordering materials in bulk and saving on design costs, homebuilders can pass those savings onto buyers, making homes more affordable.
However, building homes in factories comes with its challenges. First, there is the upfront investment required to establish a factory and the workforce needed to operate it. This type of homebuilding has also proven to be vulnerable during economic downturns. Modular home production in Vermont has already seen a decline since the 2008 housing crash, and several factories shut down during that time. For instance, the Fair Haven plant, which closed in 2011, was one of many casualties of the housing market collapse.
Housing Commissioner Alex Farrell expressed caution about the state investing too much public money in off-site construction. “We need to be thinking about that eventual bust cycle... we just don’t want to leave the state holding the bag,” Farrell said, acknowledging the potential risks involved.
Despite these risks, there are already some initiatives underway to jumpstart the factory-built housing industry in Vermont. Some developers, like Summit Properties, have already begun purchasing modular homes for new developments. “It boils down to cost,” said Zeke Davisson, Summit’s chief operating officer, referring to the company’s decision to use modular homes for a new mixed-income housing development in Middlebury. Summit estimates that choosing modular homes will save up to 10% on construction costs.
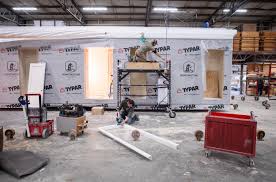
Furthermore, Vermont state leaders are exploring ways to increase factory capacity by offering incentives to boost off-site production. One proposal involves supporting the reopening of the Fair Haven plant, which could help address the ongoing housing crisis.
While factory-built homes offer a promising solution, many are still hesitant due to concerns over long-term viability and sustainability in a fluctuating economy. However, the urgency of Vermont’s housing shortage may make this innovative construction method one of the few options available to meet demand while keeping costs manageable.
As the state grapples with its housing challenges, the future of off-site construction remains a critical conversation. It’s clear that without significant changes to the housing production process, Vermont’s housing crisis will continue to deepen, and the need for bold solutions like factory-built homes has never been more urgent.
The smartest construction companies in the industry already get their news from us.
If you want to be on the winning team, you need to know what they know.
Our library of marketing materials is tailored to help construction firms like yours. Use it to benchmark your performance, identify opportunities, stay up-to-date on trends, and make strategic business decisions.
Join Our Community