How Will Tariffs Impact the Construction Industry in 2025?
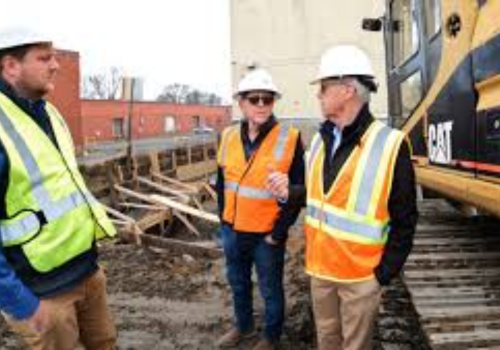
Since President Trump took office, the introduction of various tariffs on imported goods has significantly altered global trade dynamics and affected the U.S. economy. Below is an overview of the latest changes to tariff policies and Dodge's preliminary outlook on how the construction industry may be impacted this year.
In the Q1 2025 forecast, Dodge initially anticipated that the U.S. tariff rate would rise from 3% to 10% by the year's end, based on insights from Moody's Analytics. However, as Dodge compiles its updated assumptions for the next quarterly forecast, it now believes the trajectory of these tariff changes will be different. As of March 12, the average U.S. trade-weighted tariff rate has already reached 8.1% (Wells Fargo). Moody's Analytics now projects the effective tariff rate to peak in Q2-2025, not Q4 as previously expected. Rather than hitting 10%, if all current and proposed tariffs are enacted this year, the effective tariff rate is forecast to rise to 12%.
.png)
Here’s an update on the latest tariff policy changes and retaliatory measures (as of March 12, 2025):
- As of March 4, the U.S. imposed a 20% tariff on all imports from China. In response, China has placed a 15% tariff on select goods (including coal, LNG, and various food and animal products) and a 10% tariff on items like crude oil and agricultural machinery. Additionally, China plans to block 15 U.S. companies from purchasing Chinese goods without approval.
- On the same date, the U.S. levied a 25% tariff on all imports from Mexico, excluding goods covered by the USMCA (which will also face a 25% tariff starting April 2). A 10% tariff has also been imposed on potash (fertilizer), with Mexico set to announce retaliatory tariffs on April 2.
- The U.S. also enacted a 25% tariff on all imports from Canada, excluding USMCA-covered goods, which will be subject to a 25% tariff starting April 2. A 10% tariff on energy products (such as crude oil and natural gas) and potash has been placed as well. Canada retaliated on March 4 by imposing tariffs on $21 billion worth of U.S. goods.
- Additionally, the Trump administration has indicated its intention to impose a 25% tariff on copper and lumber, although this has yet to be implemented.
- The U.S. placed a 25% tariff on all steel and aluminum imports as of March 12, prompting Canada to retaliate with new tariffs on a cumulative $42 billion worth of U.S. goods, including steel and aluminum.
- On February 26, the U.S. proposed a 25% tariff on all goods from the European Union, though this has not been finalized. The EU has since announced its own tariffs on $28 billion of U.S. goods, effective April 1.
- On March 4, President Trump declared his intent to impose reciprocal tariffs on countries that levy tariffs on U.S. products, with implementation set for April 2, though experts suggest it could take months for these changes to take effect.
The construction industry will face the most immediate risk from rising material prices. If producers cannot find alternative inputs or suppliers, or if they do not receive exemptions, U.S. construction will see higher input costs. A significant portion of U.S. imports, approximately 41%, comes from Canada, Mexico, and China.
Construction input costs have remained approximately 40% higher than in February 2020, according to the Bureau of Labor Statistics. Unlike the tariff increases of 2018/2019, producers and consumers currently have limited ability to absorb further price hikes in an already high-inflation environment. This could disproportionately impact small and medium-sized businesses, which have less capacity to manage higher costs. Strong demand in both residential and non-residential markets will also continue to exert upward pressure on prices.
Steel and Aluminum Prices
According to the U.S. Department of Commerce, the U.S. imports about 40% of its aluminum and 25% of its steel from Canada, with an additional 12% of its steel coming from Mexico. The 25% tariffs imposed on steel and aluminum imports as of March 12 are likely to raise costs for manufacturers relying on these materials, which are widely used in construction projects.
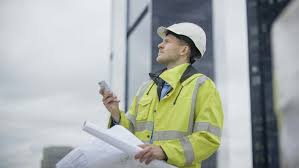
In 2018, when similar tariffs were imposed, U.S. steel production increased by 6 million tons and aluminum production rose by 350,000 tons. However, construction, manufacturing, and transportation sectors faced higher input costs and slower growth, according to a 2019 Federal Reserve study. With broader tariffs affecting both raw materials and finished products, there is an increased risk that construction projects could be delayed or canceled as owners and developers worry about uncertain pricing and potential supply chain disruptions.
The median time for a nonresidential project (worth between $20-$500 million) to progress through planning is already 6.5 months longer in 2025 than in 2019, according to Dodge Construction Network.
Automotive Manufacturing Costs
A 25% tariff on cars and auto parts will come into effect on April 2. Dodge reported a 33% drop in the dollar value of manufacturing starts in 2024, which was mainly driven by delays and cancellations in electric vehicle and battery plant projects. Further tariff-induced price increases could raise costs for vehicles imported from Canada and Mexico, as well as for those assembled in the U.S. that rely on components from these countries.
Semiconductor Chip Prices
There has been an increased focus on semiconductor manufacturing, with several new facilities slated to begin construction in 2025 and 2026, supported by incentives from the CHIPS and Science Act. However, there is a risk that tariff increases on semiconductors could raise costs for manufacturers of various U.S. products like automobiles and home appliances. Domestic semiconductor production may eventually benefit in the long term, but the U.S. will still need to rely on foreign manufacturers for a significant portion of its chip production for years to come.
Residential Materials
On March 1, President Trump signed an Executive Order to investigate the national security risks posed by timber and lumber imports, with a similar order signed on February 25 regarding copper imports. These moves increase the likelihood of further tariffs on these materials in 2025, which could further raise costs for homebuilders. More than 70% of U.S. imports of softwood lumber and gypsum come from Canada and Mexico, and a 1.2 million-unit undersupply in the U.S. housing market could worsen if tariffs slow down construction.
As homebuilders face higher costs, home prices are likely to rise, making housing even less affordable, while mortgage rates remain between 6-7%.
Macroeconomic Implications
Dodge is still analyzing the full effects of tariffs on the economy and the construction industry. If tariffs are temporary and used as negotiation tools with Canada and Mexico, the industry may not face significant downside risks. However, recent communication from the Trump administration indicates that broad, long-term tariffs are a priority, which could drive inflation higher.
With inflation relatively stable, Dodge expects the Federal Reserve to maintain interest rates in 2025 before cutting rates by 50 basis points in September and December.
The uncertainty caused by the rapidly changing policies is also reflected in the NFIB Small Business Optimism Index, which has shown high levels of uncertainty among small business owners. Many owners and developers may delay project decisions until there’s greater clarity on policy.
GDP and Growth Outlook
Moody’s Analytics now forecasts GDP growth at 1.9% in 2025, down from the 2.2% projected in January. Further deceleration is expected in 2026, with the impact of tariffs on the construction industry becoming more significant toward late 2025 or early 2026.
Reshoring
While some domestic manufacturers may benefit from higher tariffs, many will face higher input costs and greater vulnerability to supply chain disruptions. Reshoring manufacturing is complex and requires significant investment, making it unlikely that it will have a major impact on the industry in 2025. However, if the administration enacts policies to allow more skilled workers into the U.S., this could help support the industry.
Construction Outlook
Despite these risks, Dodge forecasts 10% growth in construction starts in 2025, with strong performance from the U.S. economy in 2024. Sectors like data centers, public infrastructure, and healthcare will continue to provide support for the industry. However, the residential and commercial real estate sectors remain highly sensitive to tariffs, higher costs, and changes in interest rates.
In conclusion, while tariffs will likely lead to price increases and supply chain disruptions, the construction industry remains poised for growth, supported by strong demand in key sectors and ongoing mega-projects.
Originally reported by Sarah Martin in Dodge Construction Network.
The smartest construction companies in the industry already get their news from us.
If you want to be on the winning team, you need to know what they know.
Our library of marketing materials is tailored to help construction firms like yours. Use it to benchmark your performance, identify opportunities, stay up-to-date on trends, and make strategic business decisions.
Join Our Community