Building a Better Future: Can Modular Construction Solve Canada's Housing Crisis?
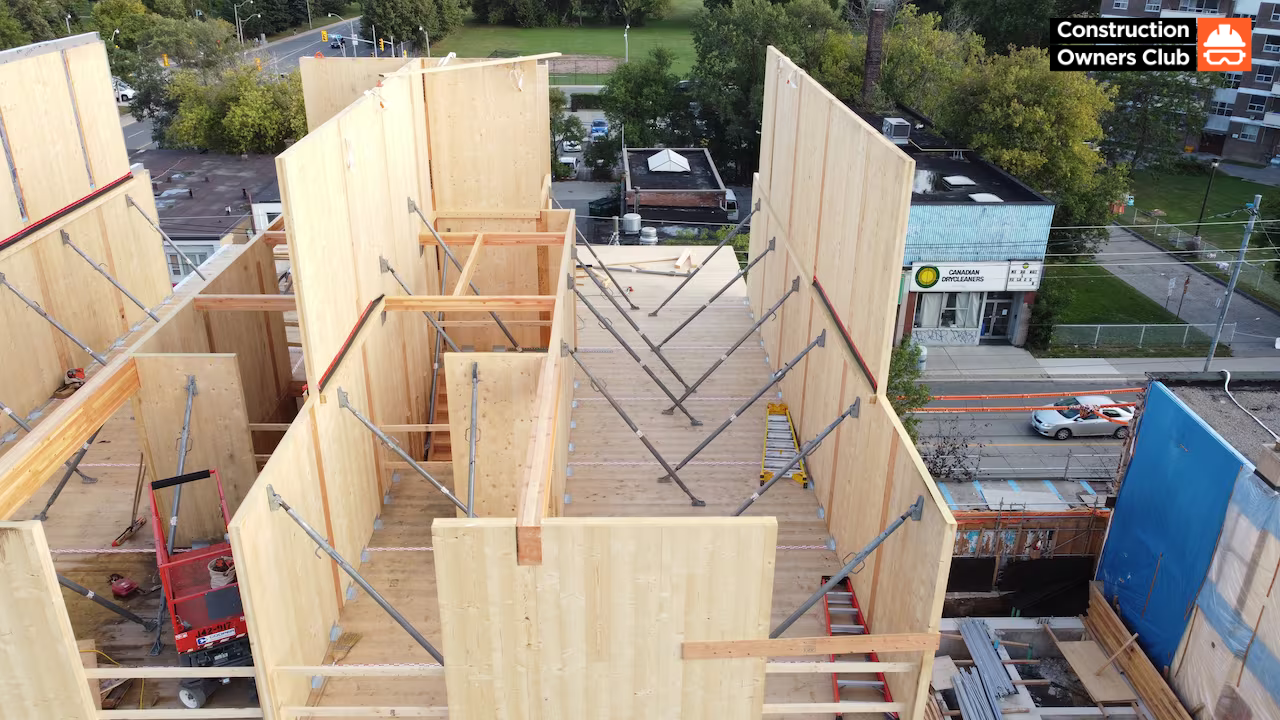
This innovative approach involves building sections of a home off-site in a controlled factory environment before transporting and assembling them on the foundation. Proponents of modular construction argue it offers several advantages over traditional methods, including:
- Faster construction times: Factory assembly allows for streamlined production and avoids weather delays, potentially cutting construction times in half.
- Improved quality: Controlled factory settings often boast stricter quality control measures compared to on-site construction.
- Enhanced efficiency: Prefabrication minimizes waste and reduces on-site labor costs.
- Streamlined approvals: Pre-approved designs and certified components can expedite the building permit process.
Government Action: A Modular Mindset
Recognizing the potential of modular construction, both federal and provincial governments are taking steps to pave the way for its wider adoption.
- The Federal Budget:
- Homebuilding Technology and Innovation Fund: A $200 million initiative aimed at advancing innovative construction methods, including modular housing.
- Low-cost financing: $500 million allocated through CMHC's Apartment Construction Loan Program to support the development of prefabricated apartments.
- Catalogue of pre-approved designs: A federal investment is facilitating the creation of a catalogue showcasing pre-approved low-rise housing designs, potentially suitable for modular construction.
- Provincial Initiatives:
- Ontario: The province is actively studying the feasibility of modular construction within its borders. They are engaging with industry experts to gather insights and explore strategies for deploying modular housing solutions.
- Red Tape Reduction: Both federal and provincial governments aim to address building approval delays, a significant hurdle for traditional construction. Efforts include streamlined inspections and collaboration with municipalities. Canada's housing shortage is a pressing issue, with skyrocketing prices and limited availability leaving many struggling to find a place to call home. But a potential solution is emerging: modular construction.
Challenges and Considerations
While modular construction offers exciting possibilities, challenges remain. North America lags behind other developed countries in its adoption of this method. Experts emphasize that simply replicating traditional construction practices in a factory setting isn't enough.
Chris Hill, founder of BCollective Homes and BOSS (an open-source modular design resource), stresses the importance of embracing true innovation, not just replicating old methods. Prefabrication offers opportunities to improve efficiency and sustainability in ways not achievable on-site.
Finding the Right Fit: Balancing Automation and Regional Needs
The optimal level of automation in modular construction will likely vary depending on regional considerations. Supply chains, production capabilities, and local market needs will all play a role.
A Collaborative Path Forward
There's no single solution to Canada's housing crisis, but modular construction offers a promising avenue for progress. Continued government investment, industry collaboration, and a commitment to innovation are all essential to unlocking its full potential.
Building a better future means building more homes. While modular construction isn't a magic bullet, it can be a powerful tool in our collective toolbox. With a forward-thinking approach, Canada can leverage this innovative technology to create more attainable and sustainable housing for all.
The smartest construction companies in the industry already get their news from us.
If you want to be on the winning team, you need to know what they know.
Our library of marketing materials is tailored to help construction firms like yours. Use it to benchmark your performance, identify opportunities, stay up-to-date on trends, and make strategic business decisions.
Join Our Community