ON THE LEVEL: VJS’ Rick Andritsch elected vice president of AGC of America
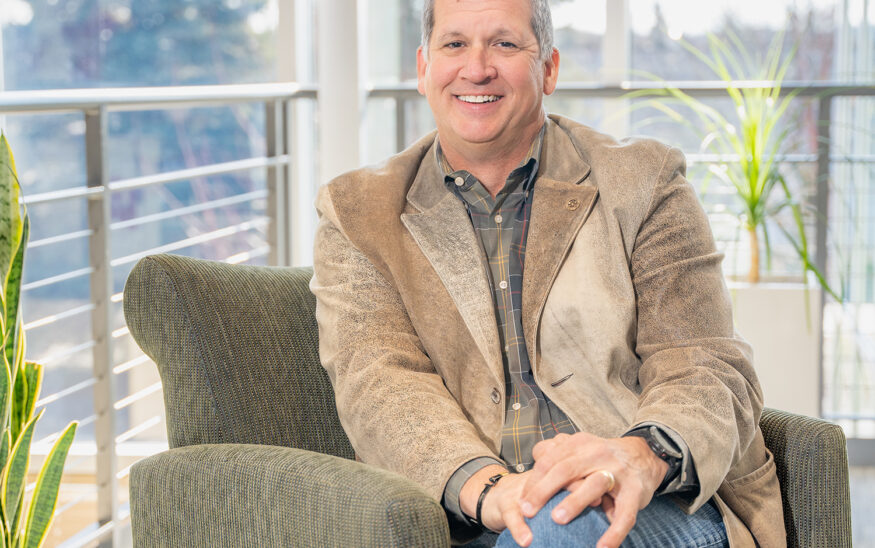
Rick Andritsch, vice president of business development at Pewaukee-based VJS Construction Services, has been elected the vice president of the Associated General Contractors of America. He is the first person in the state of Wisconsin to be the chair of the organization’s building division and serve AGC on the national level.
“I’m honored, humbled and proud to represent Wisconsin, AGC of Greater Milwaukee, AGC of Wisconsin and VJS Construction Services to be the part of voice of construction not only here but AGC nationally,” Andritsch said. “I will be the voice in three years, but I’m part of the team of the voice right now.”
In 2000, Andritsch first got involved in AGC national while working in business development for VJS. He has served on several national committees and chaired the Business Development Forum. In 2014, he was elected chairman of AGC’s Building Division and served on the National Board of Directors.
After serving in the Building Division, Andritsch joined the Public/Private Industry Advisory Committee (PIAC) as chair and met with large clients, including Target, Home Depot and Johnson & Johnson. He also served as co-chair of the AIA-AGC Joint Committee, working directly with architects and tackling issues concerning both contractors and architects.
“If I get involved, I jump in at the deep end,” Andritsch remarked about his experience. “I needed to be a sponge and learn from a lot of people. We talked with competitors and asked, ‘How do you do this? How do you get work?’ and interacted with people at different ages and levels. The organization has morphed from an older crowd to something more diverse.”
Andritsch encouraged readers to reach out to him about any hot topics.
Questions and answers have been edited for style and brevity.
The Daily Reporter: What are some highlights in your career with AGC of America to date?
Rick Andritsch: What I loved about the PIAC is I was one of 10 contractors in the room with about 25 owners sitting around the table. The owners come to those meetings saying, ‘Here’s the issues we have with contractors, the issues we have with architects, the issues we have with contracts. How do we get around those issues?’ It became a very risk-oriented discussion.
I would have never had the opportunity to sit with 25 owners who build every day and talk about what they don’t like about our contracts, how we change that and how we change the wording in our contract to become more accommodating to them but not give up everything. That was an eye-opening experience.
Public-private partnerships (P3) are a type of delivery now. That wasn’t prevalent at all, except for some big owners like Johnson & Johnson, when they perform a billion-dollar contract, they do P3s. They get in the room and tell us, ‘Here’s what’s going well with this and here’s what’s going bad.’ And how we change these moving forward. This was 12 years ago and now P3s are more prevalent. Having those conversations have helped with owners who do large projects.
In the AIA-AGC Joint Committee, one highlight we had with them is helping put together “Walk a Day” in my shoes. What that means is an architect will come to a contractor’s office on a hard bid day and live the pain of going through a bid day with us and see what we go through. Then, we might go to an architect’s office and sit through a design charette with one of their owners.
The owners tell them what to do and we see what the architect comes up with – from no idea of what the building should look like to a design charette at the end of the day turned into drawings. You get empathy for each other and that was a real success from the AIA-AGC Joint Committee.
Another success was talking with academia and trying to push school with construction management and architecture students and tell them we need to teach collaboration in school before you graduate. When you hire an architect, an engineer and a contractor who are going to work for three different firms, we throw them in a room together and tell them to figure it out.
The point to this was to have two or three classes during their program that collaborates with engineers, architects or contractors. Or have a capstone project where these people must work together and have empathy for each other and what they do. It’s still a movement in the industry.
TDR: What are some of the key issues of the industry today?
Andritsch: Workforce is a major conversation. It’s on the top of the list nationally and locally. Construction in Wisconsin is a seasonal game and there is a lot more work going on in the summer than in winter. But you start a lot of jobs in the summer and close buildings in so you can do them in the winter. But the busier we get, finding workforce can be tough.
There’s a lot to talk about with work in Mount Pleasant that will be going on. It’s been announced Microsoft is coming with a data center and that’s going to require a lot of workers over the years. When you have that many people working in one spot, that takes away from other spots. We need to be careful and bring in as many workers as we can back into the industry.
Workforce isn’t just for today, tomorrow or the next five years. We need people in grade school, middle school and high school to realize this is great career. You don’t need to be just out of college to be a project manager or estimator. You can come right out of high school, get in an apprentice program and become a carpenter. In five years, when you’re a journeyman carpenter, you can make $100,000 a year. After that you can open your own business.
There are so many success stories. So many people can come out of high school and start a great career in the trades – as a plumber, electrician, carpenter, fitter, you name it. All of those are special skills and those skills aren’t going to go away, even with artificial intelligence in the future. You’re not going to build a big enough machine to pour a hospital or a university.
Our jobs may change over time, but you still need skilled people who understand how things are built. Not just management, but how things go together and connect.
Another big issue we’re dealing with is mental health in construction. There are more suicides in the construction industry than any other industry. We are doing things locally with the mental health committee with ACG of Greater Milwaukee and some of our insurance companies and large contractors to help make the stigma go away.
On a national level, we need to bring all these together and share these stories so the other states can see what we’re doing really well, and say, ‘Here’s a great program in Wisconsin, a great program in Atlanta, a great program in Texas. Let’s share these at a national convention level.’ There’s going to be 85 other chapters going, ‘We need to do this too.’
TDR: What are the exciting technological developments in the construction industry?
Andritsch: One example is design-build. We had a meeting with a client about a new potential project. The contractor and architect were at the table with the owner, and we used an AI software that basically designs a building with certain parameters.
We fed it parameters, such as the acreage of site, setback requirements, density requirements, parking requirements by room and where parking will go. … The program automatically does the calculations and can show what rent and performance will be. We were changing the performance in seconds with this system. The owner was really impressed with it.
That’s more on the architectural side, but it has estimating and change of architecture. It changes the shape of construction and developer’s performance all wrapped in one product. We probably went through 40 options in an hour and a half meeting. Typically, that would be back and forth in four or five different meetings.
There’s going to be technology on site. At an annual convention we saw a safety dog walking around. There will be robots on job sites going 24/7 looking for safety issues. Some of these robots can check your temperature while they’re going by. You might be spiking a fever and it will give a warning to take a break.
The robot will be able to send safety violations to the subcontractor or superintendent or safety director. A robot can mark lines at night for a drywall installer and save all that labor figuring that out. Technology is coming faster and faster, but you must weigh the value of it.
If it’s a big job some of these makes sense. But for a smaller job, it might not make sense to program a robot. You have to know when and when not to use it.
A couple of years ago, a demolition contractor we worked with used a robot for the job. The operator had a joystick and stood on a scaffold outside the second floor doing demolition work. The robot pounded on the wall, stuff dropped off and it scooped it into the chute to the dumpster. It was doing what four people could do together. It was four times as efficient as manpower could have been in that situation.
Think about the person running the machine. That’s probably someone who went to school for gaming for example and understands how to run a piece of software. You’re creating new opportunities in construction and new job titles.