Tariffs Reshape Project Financing and Delivery in Construction Sector
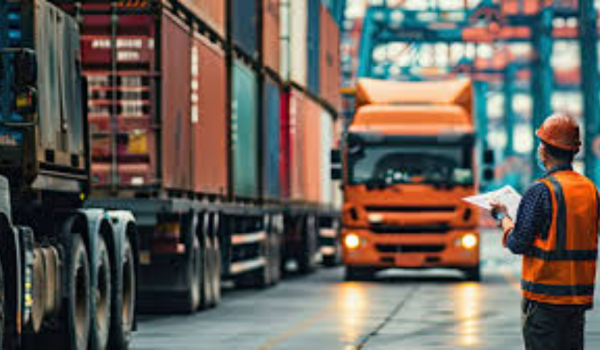
The construction industry is undergoing a major shift as rising material costs — driven largely by tariffs enacted during President Donald Trump’s administration — continue to reshape how projects are financed, structured, and delivered. Brian Gallagher, vice president of corporate development at Graycor, a general contractor based in Oakbrook Terrace, Illinois, writes that the financial impacts go far beyond simple cost increases.
Material Costs Upend Budgeting and Risk
Tariffs on essential construction inputs like steel, aluminum, and lumber are fueling a new era of volatility in development. These rising costs are layering on top of post-pandemic inflationary trends, significantly impacting commercial real estate — particularly in the industrial and manufacturing sectors.
“These dynamics are not just squeezing budgets; they’re fundamentally altering how deals are structured, how risk is evaluated and how projects are executed,” Gallagher wrote.
As overall project costs climb, lenders and investors are being forced to reevaluate their approaches. Gallagher notes that this shift is changing key financial metrics such as loan-to-cost ratios and debt-service coverage, and borrowers are having to secure more capital — whether through additional debt or increased equity injections.
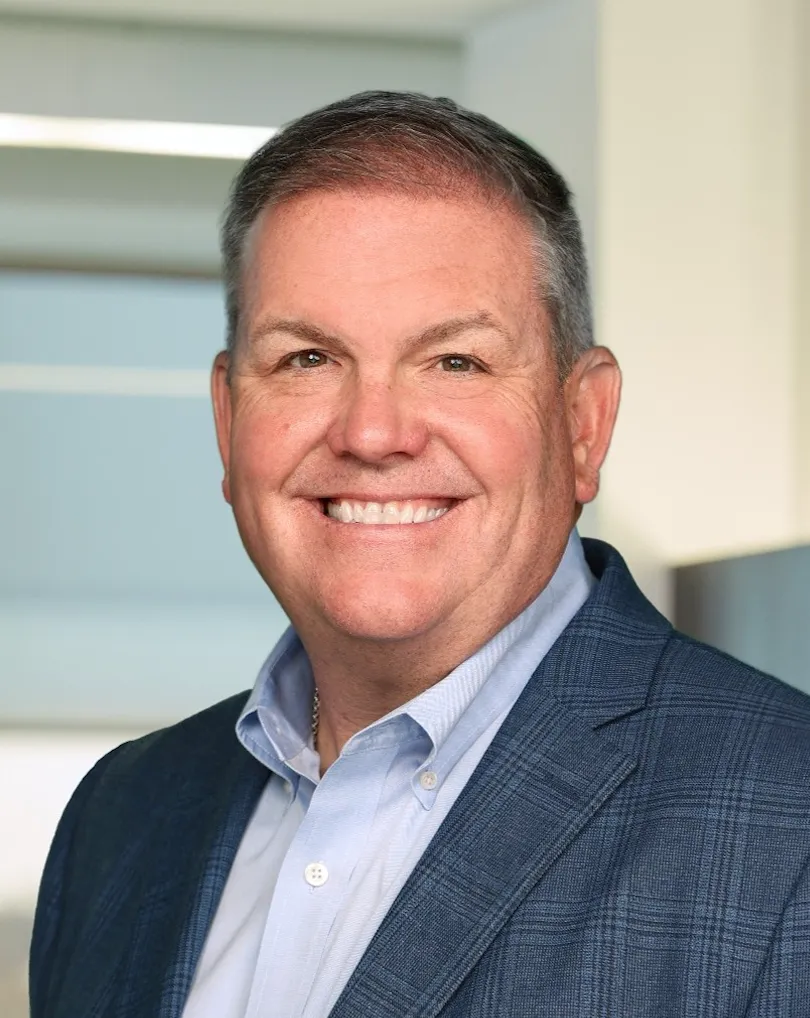
“In response, financial institutions are adjusting their underwriting models,” he said. “Many are requiring more detailed cost escalation strategies, larger contingency budgets and earlier confirmation of contractor pricing.”
Financing Gets More Complex
The increasing cost of construction is not only impacting financial assumptions but also altering timelines and deal structures. In some cases, lenders and investors are becoming more active participants in project planning — including weighing in on which contractors are selected.
“Some projects are seeing delayed closings or restructuring of deal terms, as initial pro formas no longer ‘pencil out’ under the pressure of higher inputs,” Gallagher explained.
In addition to altering the debt and equity mix — or “capital stack” — developers are being asked to assume more upfront risk. This is especially true for new developments in uncertain or slower-moving markets.
“Lenders are becoming more conservative, while equity investors are being asked to absorb greater upfront risk,” he noted.
Early Procurement and Cash Flow Pressures
Volatility in material pricing is also disrupting cash flow. Gallagher explains that developers are accelerating procurement schedules for key materials like structural steel, mechanical equipment, and electrical gear in order to lock in prices and avoid supply chain delays.
“Materials that may have once been ordered mid-project are now being purchased as early as possible to lock in pricing and ensure availability,” he wrote.
This early spending is compressing traditional draw schedules and placing more liquidity demands on developers earlier in the project timeline. For sectors like manufacturing, which often require heavy and specialized equipment, the effect is even more pronounced.
“If developers aren’t strategic in managing cash flow, one project’s acceleration can jeopardize the broader portfolio’s liquidity,” Gallagher warned.
Evolving Strategies for a New Era
The industry is responding with smarter, more proactive planning. Gallagher points to a number of strategies developers are using to regain control, including early contractor involvement, collaborative delivery models, and better risk-sharing contract terms.
“Preconstruction is no longer viewed as a planning step, but as a vital tool for financial control and project viability,” he said.
Developers are also increasingly using design-build and construction manager-at-risk models to create better alignment across design, cost, and delivery timelines. Guaranteed maximum price (GMP) contracts that include escalation clauses are gaining popularity, providing a financial buffer for unexpected spikes in material costs.
Procurement is also evolving: “Some owners are warehousing materials, purchasing early and storing on or offsite to ensure both cost and schedule certainty,” Gallagher added.
Sector-Specific Impacts
Not all construction sectors are impacted equally. High-return industries like industrial, manufacturing, life sciences, and data centers are better positioned to absorb rising costs due to their strong underlying value propositions — such as proximity to logistics hubs or critical infrastructure.
On the other hand, sectors like speculative office, retail, and hospitality — which often operate on thinner margins and face less predictable demand — are seeing increased delays, cancellations, or a pivot toward renovating existing structures.
A Shift Toward Flexibility and Resilience
Developers and investors are placing a premium on flexibility. Projects that can adapt — through phased delivery, scope adjustments, or material substitutions — are more likely to secure financing and move forward.
“Projects with flexible designs and proven delivery partners are seeing stronger support,” Gallagher wrote.
Many investors are also shifting away from new builds and toward renovation projects, which tend to be more cost-predictable and require fewer raw materials.
The Bigger Picture: Policy and Agility
The duration of the current cost challenges remains uncertain and largely dependent on national and global trade policy. Gallagher notes that efforts to increase domestic production of materials like steel and electrical gear may eventually help, but such solutions are long-term.
“In the short term, construction and development professionals must operate with agility,” he wrote. “That means strategic procurement, diversified supply chains, strong contractor relationships and financial models that can absorb more front-end risk.”
He concludes with a broader warning: “Rising material costs due to tariffs are not simply a budgetary concern — they’re a structural shift in how commercial projects are conceived, financed and delivered. For those who adapt quickly and build resilient partnerships, this disruption presents an opportunity.”
Originally reported by Brian Gallagher in Construction Dive.
The smartest construction companies in the industry already get their news from us.
If you want to be on the winning team, you need to know what they know.
Our library of marketing materials is tailored to help construction firms like yours. Use it to benchmark your performance, identify opportunities, stay up-to-date on trends, and make strategic business decisions.
Join Our Community