Poettker Construction’s Drone Program Enhances Safety and Productivity
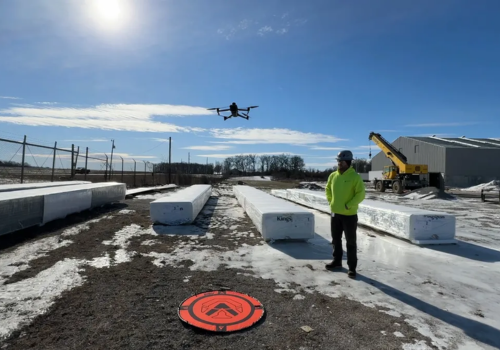
Poettker Construction, based in Breese, Illinois, has successfully integrated drones into its operations as a "jack of all trades" tool, helping with everything from inspections to marketing, safety, and photography. The company launched its drone program in February, and the results have already paid off, benefiting both field workers and those in the office.
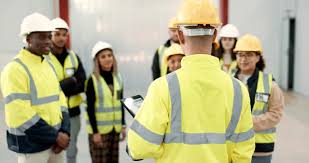
In a recent interview with Construction Dive, Charles Wilson, Poettker’s Vice President of Risk Management, and Logan Decker, the operator managing the drone program, shared insights on how the program began, overcame challenges, and provided valuable advice for other builders interested in adopting drone technology.
How did Poettker's drone program get started?
CHARLES WILSON
“We realized that utilizing outside resources for inspections could get costly. There’s a return on investment if we own our drone equipment and have an in-house operator. Plus, owning the data gives us more control and flexibility.”
When deciding to bring the drone program in-house, Poettker chose to integrate it with the risk management department. Wilson explained, “We saw the opportunity to drive down rework, promote better workmanship, and, ultimately, enhance safety. The drone program also supports other initiatives, like safety, quality, and production.”
How is the drone technology deployed across these areas?
WILSON
“For safety, we can inspect elevated areas without putting someone at risk. We use drones to identify hazards from the air. For quality, our staff can review footage of project sites and definable work features, allowing them to cover more ground and monitor work in real time.”
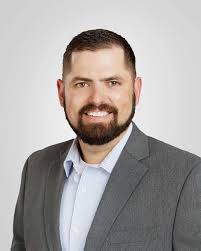
The drones also help with marketing efforts by capturing high-quality aerial images and footage, showcasing Poettker's projects.
What were the challenges in implementing the program on job sites?
LOGAN DECKER
“Introducing new technology usually gets some pushback. People tend to stick with the systems they’ve used for years, but the program has been well-received overall. We focus on making sure everyone knows the drones are available for their use, and it’s a gradual process of increasing the number of flights and frequency.”
WILSON
“One challenge we faced was underestimating how quickly the program would grow. We had to create a scheduling system to ensure timely drone service for everyone. At times, we had to remind ourselves that we are a construction company with drones, not a drone company doing construction.”
If you were to restart the program, what would you do differently?
WILSON
“The technology evolves rapidly, and there were times we had to adjust. My advice is to understand your company’s needs and those of your clients, and secure buy-in from stakeholders. Training was critical for us when purchasing equipment. We made sure to get professional training on the equipment, which was essential for understanding both the tech and its practical application.”
DECKER
“Stay on top of software updates. Drone software is constantly improving, and keeping up with updates ensures that the equipment is functioning at its best, giving us better data and improving efficiency.”
Poettker Construction's drone program has proven to be a valuable tool for improving safety, productivity, and project quality. By staying grounded in construction fundamentals while embracing technology, Poettker has successfully integrated drones into its workflow and is reaping the benefits. As Decker mentioned, “The more you stay on top of these updates, the better product it will deliver to your team, customers, and stakeholders.”
Originally reported by Matthew Thibault in Construction Dive.
The smartest construction companies in the industry already get their news from us.
If you want to be on the winning team, you need to know what they know.
Our library of marketing materials is tailored to help construction firms like yours. Use it to benchmark your performance, identify opportunities, stay up-to-date on trends, and make strategic business decisions.
Join Our Community