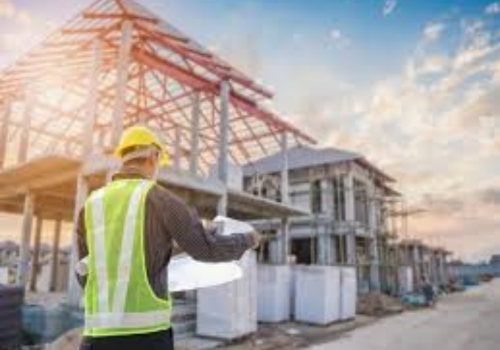
Providence, RI – The future of residential construction? According to industry professionals gathered at the JLC Live Residential Construction Show, there’s one word that keeps coming up—plastics.
A line from The Graduate, the 1960s classic film, may have been ahead of its time. In 2025, plastic isn’t just a buzzword—it’s become a foundational element in many of the latest building materials, offering strength, sustainability, and versatility in construction applications.
The annual JLC Live event, held March 28–29 at the Rhode Island Convention Center, brought together builders, vendors, and innovators from across the country. The air was filled with the scent of sawdust and the sound of power saws as new materials and methods took center stage.
Why Plastics? Why Now?
The driving force behind many of the innovations seen at JLC Live is the rise of composite materials—engineered blends made from two or more materials, often stronger and more durable than the originals. Most of the composites on display use plastic—specifically high-density polyethylene (HDPE)—as a binding agent.
“Most new composite materials for residential construction are composites. The binder in these composites is some form of plastic, usually a high density polyethylene,” one vendor explained.
.jpg)
Look around your garage or recycling bin, and you’ll probably find HDPE—it’s marked with a “2” inside the recycling triangle, and it’s what your standard 5-gallon bucket is made from.
But why not stick with wood? While wood is still widely used—especially pressure-treated lumber for decking and framing—it has limits. It’s vulnerable to moisture, rot, pests, and structural degradation over time.
“For framing, [wood] cuts the price in half compared to steel or aluminum, but it only lasts half as long. For many decking material suppliers, that means their product long outlasts the thing holding it up.”
Turning Agricultural Waste Into Building Materials
One of the standout products came from Mississippi-based Modern Mill, which showcased “Acre,” a composite building material designed for siding, decking, and fencing. What makes Acre unique is what’s inside: rice husks—agricultural waste repurposed from local farms.
“The composite is made like the others, with plastic as a binder, but the material being held together is rice husks from farms a few miles down the road from the manufacturing plant,” said Sales Director Chandler Delinks.
Rice hulls, already used in filtration, paper, and growing mediums, also offer a pleasing grain to the finished product.
“The composite with rice hulls was originally developed to replace tropical hardwood. The hulls give the composite a grain,” Delinks explained.
Stone and Plastic: Decking That Lasts
Also gaining popularity is mineral-based composite decking, a material made from crushed limestone and plastic. On display at the Deckorators booth, it drew attention not just for its durability but also for its non-slip texture, even when wet.
“In addition to being durable, the decking is sought after for its inherent roughness, so there's less chance of sliding when it’s wet,” said Chris Berry.
A New Era for Floating Docks
Lumberock, a major name in the composite decking world, unveiled its latest marine innovation—a two-foot-long board, designed for floating dock construction. The board took five years to design and test and responds to long-standing demand in the construction community.
“Contractors had been clamoring for the longer boards for a long time because they want to use them for floating docks, where the 16-inch boards were just too short and they had to use wood instead which quickly deteriorated,” said Jason Sparger, vice president at Lumberock.
With increased interest, Sparger said he's already added two new extruders to boost production—and expects more will be needed soon. He also noted a regional trend:
“The Northeast is always quicker to adopt new technologies than the South (where pressure-treated framing is still the norm), and he said he expects his new marine boards to be no different.”
Historic-Looking Windows That Save Lives
Among the more niche innovations was a clever product from Green Mountain Window of Rutland, Vermont. Brothers Andrew and Dave Keefe introduced a new take on a double-hung window that maintains historical accuracy while meeting modern fire code standards.
“Dave Keefe demonstrates what looks like a double-hung window that actually fully opens outward, serving as an emergency exit,” during the show.
Although a similar design was patented in 1870—meaning their version isn’t patentable—the Keefes say no one else is making windows like theirs today.
Skilled Labor: A Lingering Concern
Even with all the innovation on display, one of the most pressing issues discussed was the ongoing skilled labor shortage. In Vermont, for example, Green Mountain Window struggles to find workers as vocational programs have been cut in local schools.
“They’ve seen Vermont schools shut down most vocational programs, which helped create a pipeline of workers.”
This shortage is part of a larger concern facing the construction industry nationwide—one that no amount of innovation can solve without investing in training the next generation of builders.
Originally reported by The Providence Journal.
The smartest construction companies in the industry already get their news from us.
If you want to be on the winning team, you need to know what they know.
Our library of marketing materials is tailored to help construction firms like yours. Use it to benchmark your performance, identify opportunities, stay up-to-date on trends, and make strategic business decisions.
Join Our Community