New U.S. Tariffs Spark Uncertainty Across Construction Industry
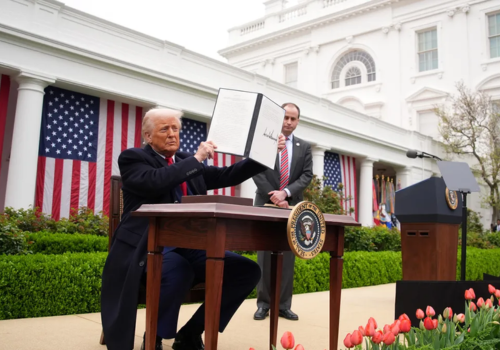
In a move that could significantly impact the construction industry, President Donald Trump announced sweeping new tariffs this week, raising concerns about future project viability and economic stability. The announcement introduced a 10% baseline tariff on imports from all U.S. trading partners, alongside harsher reciprocal tariffs — including a 34% increase on Chinese goods and 20% on European Union products.
While critical construction materials like steel, aluminum, lumber, and copper are exempt from the new reciprocal tariffs, builders are already grappling with existing import taxes. Since March 12, steel and aluminum imports have faced a 25% tariff, and Canadian softwood lumber carries a 14.5% penalty, according to the National Association of Home Builders.
“Material prices are likely to rise in the coming months,” said Anirban Basu, chief economist at Associated Builders and Contractors (ABC). “On the nonresidential side, keep an eye on prices for iron and steel products, as well as aluminum. Notably, domestic steel prices have already risen significantly.”
While contractors source materials like concrete and gypsum mostly from U.S. suppliers, broader pricing trends could still be affected.
“However, even if products are domestically produced, tariffs could affect domestic pricing or lead times,” said Tim Jed, supply chain leader at DPR Construction. “Ultimately, what matters is, where are we buying from and where are those materials being imported from, but that’s not an easy piece of information to get to.”
Project Delays and Budget Risks
Nonresidential construction material prices surged at a 9% annualized rate in early 2025, with overall input costs now 41% higher than in February 2020, according to ABC. That sharp rise, combined with policy uncertainty, could discourage future investments.
“Most construction activity will show these effects in a lagged fashion, as projects already started will largely continue,” said Jeannine Cataldi, associate director of global construction at S&P Global Market Intelligence. “It is future spending that is most at risk.”
In February, nonresidential construction spending reached an all-time high of $1.26 trillion. But Cataldi warns that publicly funded projects — the key driver behind the growth — could also face setbacks if budgets shrink due to inflation or if federal infrastructure funds are reallocated.
“Infrastructure will be impacted if funding is recalled — this is on hold currently — if rising material prices affect budgets, and the labor force is constrained by immigration policies,” she added.
Labor Market in the Crosshairs
Beyond pricing, construction labor markets are also under pressure.
“We remain very concerned about the construction labor market,” said Michael Guckes, chief economist at ConstructConnect. “With the very real possibility of a contraction in labor due to heightened unauthorized worker deportations, we could see the biggest cost concern for the industry in 2025 come not from materials but from labor.”
.jpg)
Ken Simonson, chief economist at the Associated General Contractors of America (AGC), echoed those concerns. Although increased investment in sectors like data centers, rail, and broadband may offer some buffer, tariffs could still hurt momentum.
“Copper prices have taken off recently, they’ve exploded to the upside,” Basu noted during an April 2 ABC webinar. “Data centers use a ton of copper. There are some issues emerging because of these tariffs.”
Strategic Calculations Underway
While some economists believe the tariffs could be a strategic push to lower international trade barriers, the industry is treading cautiously.
“This might be a mechanism by which to really lower tariffs against U.S. exports,” Basu said. “If that’s the end game here… as an economist, I of course love that.”
Yet for contractors, the risks are immediate and tangible. Fixed-price contracts that don’t factor in sudden material cost spikes could lead to project cancellations or scaled-back budgets.
“If contractors raise prices to account for tariffs, some owners may cancel, defer or scale back upcoming projects,” said Simonson. “But the biggest threat is from producers and logistics firms that face higher costs or lose export sales... These companies and their workers will reduce spending, including for construction.”
The tariffs' immediate implementation left many scrambling.
“Think long and hard about cashflow, and do not hold on to unnecessary cost centers for too long,” Basu advised. “Put another way, contractors should focus on retaining cash.”
Jed emphasized a measured response: “We let our teams work with the tools that we’ve built internally to look strategically on a project-by-project basis of what makes the most sense. Don’t overreact.”
Originally reported by Sebastian Obando in Construction Dive.
The smartest construction companies in the industry already get their news from us.
If you want to be on the winning team, you need to know what they know.
Our library of marketing materials is tailored to help construction firms like yours. Use it to benchmark your performance, identify opportunities, stay up-to-date on trends, and make strategic business decisions.
Join Our Community