Innovative Methods Transforming Home Construction for Speed and Sustainability
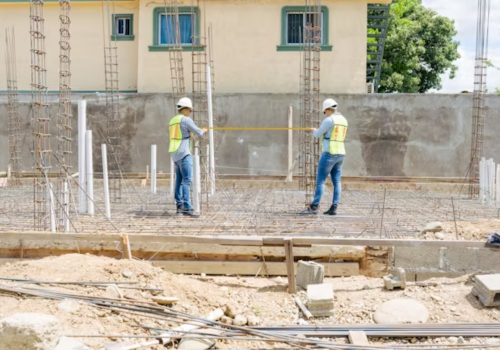
Three local companies are pioneering new approaches to building homes that are faster, eco-friendly, and cost-effective. With natural disasters, a housing affordability crisis, and limited land available for development, these innovative solutions aim to reshape the future of construction.
RENCO: Building Stronger and Greener with Composite Systems
Patrick Murphy, Managing Director of RENCO, explains the challenge of limited traditional materials:
“There are basically three materials to build with. You have steel, you have wood, and you have concrete. And that’s it. There hasn’t been a change in 100 years.”
RENCO offers a composite building system made from recycled glass, plastic, calcite, and resin. The system is designed to be stronger, faster, greener, and less expensive than conventional materials. Resembling life-size Lego blocks, these modular components allow for rapid and precise assembly.
“It’s much faster not only to build the structure, but when you are building the interior...these pieces come from a mold so they fit perfect,” Murphy said.
RENCO structures can withstand seismic activity, termites, fire, and water, with materials that are 82% greener than steel construction. A single-family home built with RENCO blocks can be completed in a day with a small team and unskilled labor.
Kobi Karp: Prefabrication for Precision and Sustainability
Architect and interior designer Kobi Karp highlights the benefits of prefabricated spaces:
“It’s a much more thoughtful way to move forward...and it’s the only way to move forward,” he said. Prefabricated rooms, built in a controlled warehouse environment, arrive fully assembled and ready for installation, reducing waste and improving efficiency. “You don’t have to go up and down elevators...the boxes that come in are disposable and recyclable,” Karp explained. Using recycled materials, Karp’s prefabrication approach minimizes reliance on external sources and ensures resilience against natural weather events.
Printed Farms: The Future of 3D-Printed Construction
James Ritter, founder of Printed Farms, is rethinking construction with 3D printing:
“The conventional methods of building were not going to meet the demands of the future and sustainability for climate impacts,” he explained.
Printed Farms has created durable, storm-resistant structures, including a Wellington equestrian facility that withstood Hurricane Milton’s tornadoes. Their 3D-printed walls, made of cement, eliminate the need for drywall and allow for creative designs.
“I can print a curved wall or a round building...at the same cost of doing something straight,” Ritter said.
While the cost of current 3D printing systems is high, Ritter envisions advancements in materials, delivery systems, and machine efficiency to make the technology more accessible.
“As it’s accepted and it grows...we are going to capture a large percentage of the market,” Ritter said, emphasizing the potential for insurance cost reductions and long-term sustainability.
A Sustainable Path Forward
These companies are driving innovation in homebuilding with materials and methods that address modern challenges, from affordability to environmental resilience. With advancements in composite systems, prefabrication, and 3D printing, the future of construction is evolving to meet the demands of a changing world.
The smartest construction companies in the industry already get their news from us.
If you want to be on the winning team, you need to know what they know.
Our library of marketing materials is tailored to help construction firms like yours. Use it to benchmark your performance, identify opportunities, stay up-to-date on trends, and make strategic business decisions.
Join Our Community