H. J. Russell & Company Leads Modular Construction Innovation in Aviation Industry
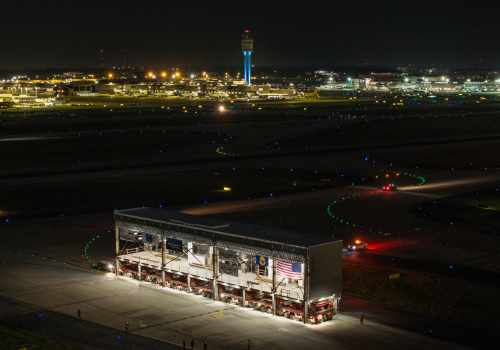
ATLANTA – H. J. Russell & Company, a major minority- and family-owned real estate development and construction services firm, is revolutionizing aviation infrastructure with its modular construction approach. As the first firm in North America to work on modular projects from program management (PM), construction management (CM), and construction management at risk (CMaR) perspectives at two domestic airports, Russell is leveraging its 70+ years of experience in airport environments to deliver efficient, cutting-edge solutions.
“By using modular construction, we've been able to reduce the total gate downtime by 46 months,” said Curtis Wilson, PMP, Vice President of Transportation & Infrastructure at Russell. This technique helps minimize disruptions at busy airports, ensuring continuity of operations while enhancing overall efficiency.
“Having PM, CM and CMaR experience allows us to come to projects with a holistic view and the keen ability to problem solve in this complex environment," said Yasmine S. Antoine, Esq., Chief Operating Officer at Russell. "Having these perspectives is extremely beneficial to future clients because we can assess, plan, and develop solutions from key learnings and hands-on experience from some of our most complex modular build projects to date."
Russell's most recent project, which began in the spring of 2024, involves serving as program manager for the $1.4 billion expansion and widening of Concourse D at Hartsfield-Jackson Atlanta International Airport. The goal is to expand the concourse while minimizing gate closures and maintaining revenue generation. The next milestone in this project is the transportation of additional building modules to the North Pier in January 2025.
The firm’s first modular project was completed in 2022 at Dallas Fort Worth International Airport with the construction of gates C35-C39, known as The High C Gates. The modular build included prefabricated 900,000-pound steel-framed units, which were transported across the airfield to their final positions at Terminal C, offering a 30% larger space with advanced technological and sustainable features.
“The benefits of modular construction within high-traffic, high-revenue environments like airports are being able to conduct the seamless transformation of the space without interrupting day-to-day operations, allowing us to successfully navigate around passenger traffic,” said Damian Lee, General Manager, Russell (Texas).
Russell’s experience spans numerous major airports across the United States, including Atlanta, Nashville, Miami, and Dallas, and extends through its sister company, Concessions International, LLC, which operates 25 airport concessions across multiple U.S. airports.
To learn more about Russell’s innovative approach, visit their website or download their e-book on the business case for modular construction at airports.
The smartest construction companies in the industry already get their news from us.
If you want to be on the winning team, you need to know what they know.
Our library of marketing materials is tailored to help construction firms like yours. Use it to benchmark your performance, identify opportunities, stay up-to-date on trends, and make strategic business decisions.
Join Our Community