Fla. Firm Cuts Costs, Speeds Rebuilding with Innovation
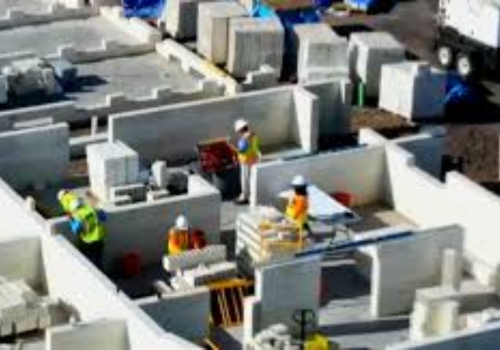
Natural disasters have the power to wipe out entire neighborhoods, leaving thousands without homes and struggling to rebuild. The recent wildfires in California, for example, destroyed over 16,000 homes and structures, highlighting the urgent need for faster, cost-effective housing solutions.
A Florida-based company, Renco, is introducing a groundbreaking technology that could revolutionize the construction industry. The company claims it can rebuild homes in just weeks, reducing costs and labor requirements significantly.
A CBS News analysis found that the price of construction materials has surged by 47% nationwide since 2016, making affordable housing even harder to achieve.
A Unique Approach to Construction
Patrick Murphy, a former Pennsylvania congressman and the managing director of Renco, oversees the company’s cutting-edge building technology. Inspired by the simplicity and strength of Lego bricks, Renco has developed a composite brick made from glass, recycled plastic, and other sustainable materials.
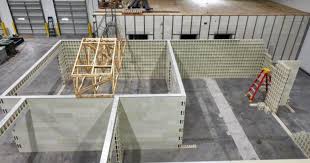
"We can basically produce about 16 homes a day in this facility," Murphy said, emphasizing the efficiency of their production process.
The company’s Jupiter, Florida-based manufacturing facility is expected to ramp up production in April, scaling operations to meet growing demand.
Strength and Resilience: How the Technology Works
Unlike traditional wood and concrete structures, Renco’s buildings are designed to withstand extreme weather conditions, including winds of up to 240 mph. The material is also highly fire-resistant and water-resistant, making it particularly suitable for disaster-prone areas.
"We decided to start in the toughest area, and so did years of testing to ensure that it could withstand Category 5 hurricanes," Murphy explained, referring to Florida as the ideal location to launch their innovative housing solution.
The real-world application of this technology is already underway. Yessica Coronado, a resident of an apartment complex near Palm Beach, Florida, had no idea her home was built using Renco’s unique construction method.
"I just thought of it as a regular apartment complex," Coronado said.
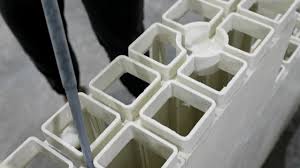
Her four-building complex, consisting of 96 units, is the first of its kind in the U.S. What makes it even more remarkable is the speed at which it was built—each building’s walls, floors, and ceilings were assembled by just eleven workers in only eight weeks.
"We built that much faster than we would have had we done it with wood or concrete, sort of a traditional material," Murphy noted.
Faster, More Affordable, and Insurance-Friendly
While the upfront cost of Renco bricks is higher than traditional materials, the overall savings are substantial due to the reduction in labor and construction time. Murphy estimates that costs are slashed by around 20% when factoring in efficiency and insurance benefits.
"We can get a lot more product built a lot faster with unskilled workers. … This entire 2,000 square foot home can be built by two people in one day," he said, underscoring the labor efficiency of their building method.
Beyond construction speed, Renco’s technology also offers long-term financial benefits. Because the buildings are resistant to rotting, rust, and termites, insurance costs for these structures are notably lower.
"They've been given such a long lifespan that the insurance on our first building is about 20% less expensive for the sort of long-term insurance," Murphy said. "It doesn't rot, it doesn't rust. Pests don't eat it, right? Termites don't eat it."
Despite its advantages, the company currently faces some structural limitations, as their technology is best suited for buildings up to five stories tall. However, as they continue to refine their methods, expansion into larger structures may be possible.
A New Era in Construction?
Experts in the construction industry believe that innovations like Renco’s could play a major role in reshaping how homes and buildings are constructed. Illya Azaroff, an architect and professor specializing in sustainable construction at City University of New York, sees this as a pivotal moment for the industry.
"Globally last year, 114 million people were displaced for natural and man-made disasters. So when I think about that, this has to be a moment of change," he said.
Azaroff acknowledges that new construction methods often come with design limitations—Renco’s modular approach, for instance, can appear somewhat blocky. However, he believes the benefits far outweigh any aesthetic concerns.
"When I see innovation in the marketplace like this, yes, we can build to fire resistance, earthquake resistance, to hurricane-force winds, tornado-force winds. We just have to have the political will to do it, and we have to have the guts to try new ways of doing things."
As housing shortages persist and climate change intensifies the frequency of extreme weather events, Renco’s approach could be a game-changer. If widely adopted, this innovative construction method could help provide stronger, faster, and more affordable housing for communities in need—turning a vision of resilience into reality.
Originally reported by Nancy Chen in CBS News.
The smartest construction companies in the industry already get their news from us.
If you want to be on the winning team, you need to know what they know.
Our library of marketing materials is tailored to help construction firms like yours. Use it to benchmark your performance, identify opportunities, stay up-to-date on trends, and make strategic business decisions.
Join Our Community